Industrial Gearbox Repair
Gearbox repairs & maintenance: We do it all!
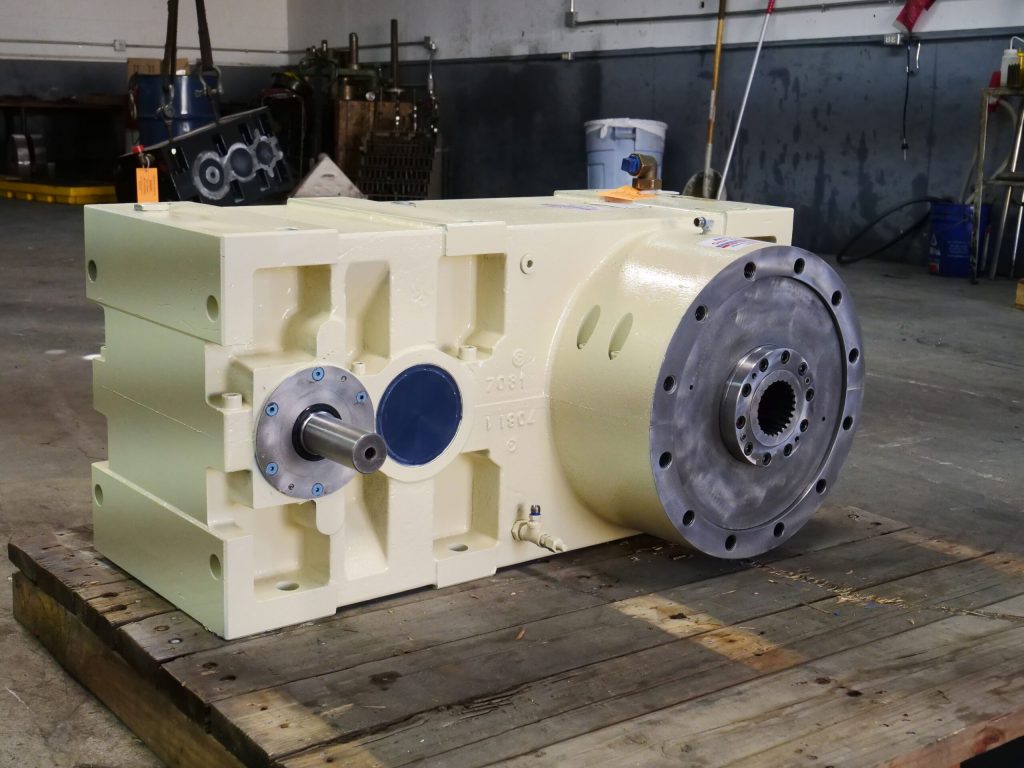
Need a Quote
Free Pickup and Delivery
Why Choose US?
Industrial Gearbox Rebuild
As a leading provider of industrial gearbox repair services, we understand the importance of minimizing downtime for our clients. Whether you’re dealing with a parallel shaft gearbox, a specific model from Baker Hughes, or one of the many types of gearboxes in the market, including Allen Gears, our team is here to help.
We specialize in repairing and manufacturing old and obsolete gearbox models that OEMs may no longer support, including those manufactured by Lufkin Gears.
We adhere to stringent quality standards in all our repair and manufacturing processes. Our emergency repair services are designed to minimize downtime and keep your machinery running efficiently. We also offer a 24-month warranty on all our services, giving you peace of mind knowing that you can trust us with your emergency gearbox repair and rebuild needs.
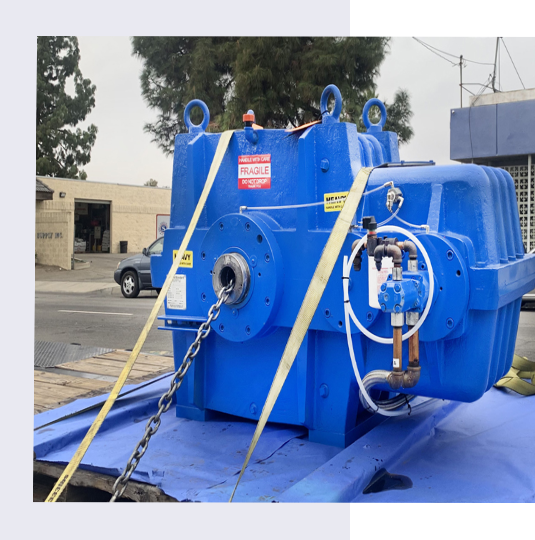
We prioritize data privacy and security, adhering to the regulations set by the GDPR. Our GDPR cookie consent plugin ensures we store the user consent and handle your data responsibly.
We Specialize in the Repair of all Gearboxes such as
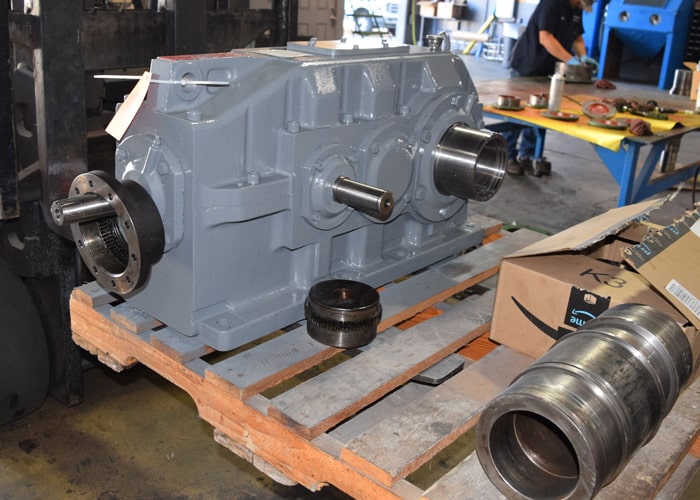
Gearbox Examination Process
At Extruder Gearbox Repair, we pride ourselves on providing a thorough and transparent repair and manufacturing process for all gearboxes.
First, our certified engineers will examine your extruder gearbox to identify any issues. We use an industrial parts washer to clean the gearbox and remove any dirt or debris to ensure the best service possible. This process helps us analyze the gearbox and determine the problem at hand.If your gearbox model is obsolete or no longer supported by OEMs, our engineers can use reverse engineering techniques to analyze and recreate the necessary components.
Our gearbox examination process is thorough and transparent. Certified engineers conduct a detailed inspection of your gearbox, utilizing industrial parts washers to ensure a clean and accurate assessment. We take pride in offering fair and reasonable price quotes based on our examination findings. If the quote is unsuitable, we provide a no-obligation option with no examination or delivery charges.
Damage and Repair Process
We are committed to providing high-quality services for all your gear repair and manufacturing needs.
Our certified engineers are experts in repairing and rebuilding gearboxes, including those with damage to casings and housings. We only use brand-new bearings and seals directly from the manufacturer, ensuring that all bearing floats and preloads are set to OEM specifications. Our Gear Manufacturing division can manufacture damaged pinions and shafts to OEM specifications with proper testing and warranty.
To ensure quick turnaround times for our customers, we keep all critical spare parts in stock, preventing delays in shipping. Once your gearbox has been reassembled, it is coated in a temperature-resistant polymer to reduce vibration and overheating and sent to our Quality Assurance Department.
Our experienced technicians run the gearbox for 6 hours under light load on a custom-built test bench in our Quality Assurance Department. This helps us identify and address any leaks, vibrations, overheating, or other operational issues. Once we have completed our testing, your Extruder Gearbox will be certified with our 24-month warranty before it is prepped for shipping.
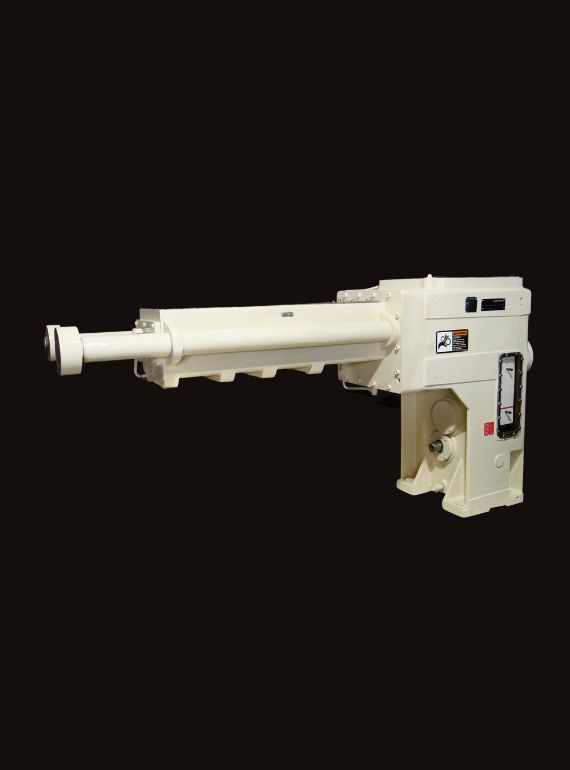
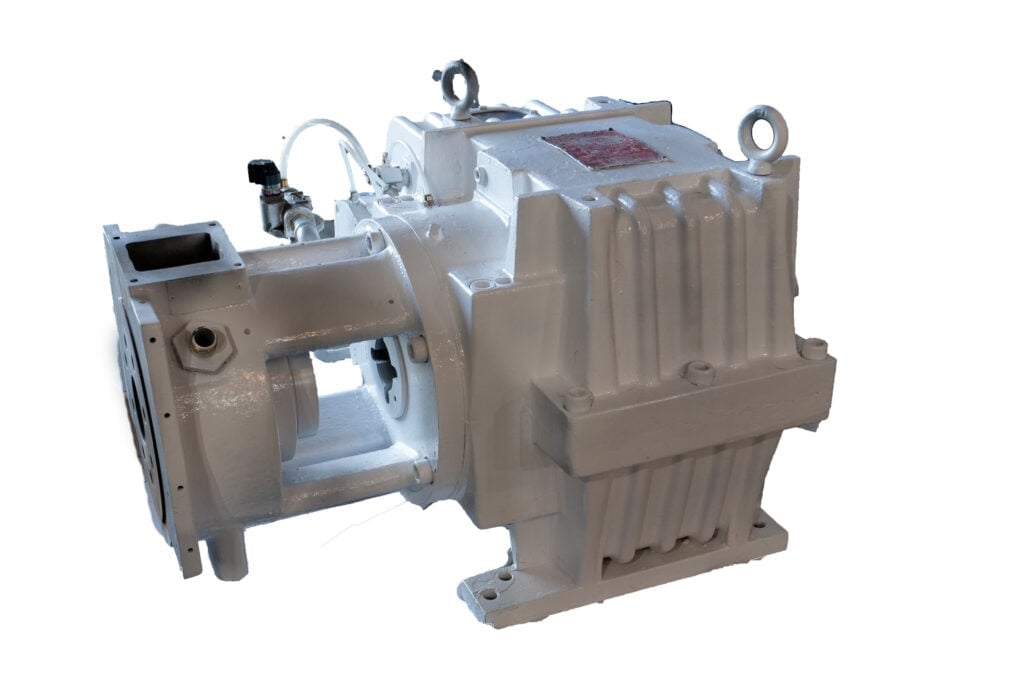
Industrial Gearbox Failure Analysis and Root Cause Determination
Industrial gearboxes play a critical role in power transmission for various sectors, such as manufacturing, construction, and transportation. However, gearbox failures are common due to their complex design and operation.
Failure can occur due to wear and tear, overheating, contamination, and misalignment, leading to losses like oil contamination, bearing failure, and gear wear. Therefore, identifying the root cause of gearbox failure is crucial to increase gearbox reliability and prevent future failures.
Effective failure analysis techniques such as non-destructive testing, vibration analysis, oil analysis, and visual inspection can be used to determine the cause of failure. Finding the root cause requires a systematic approach, considering various factors such as design, material, environment, and operating circumstances.
Preventive maintenance is key to ensuring gearbox reliability, which involves proper lubrication, alignment, and maintenance procedures. Predictive maintenance and condition monitoring are advanced technologies that can use sensors and software to predict when maintenance is necessary. By prioritizing gearbox reliability and implementing effective maintenance strategies, costly downtime and repairs can be prevented.