From automobiles to robotics, gears are necessary components of numerous machines and devices. They convert speed and torque as well as transfer power from one shaft to another. As a result, gear cutting is essential to the process of making these gears. This article will cover the various methods and their uses.
Techniques
Gear cutting involves a number of different techniques, each of which has benefits and drawbacks. The most frequently employed methods include gear hobbing, gear shaping, and gear grinding.
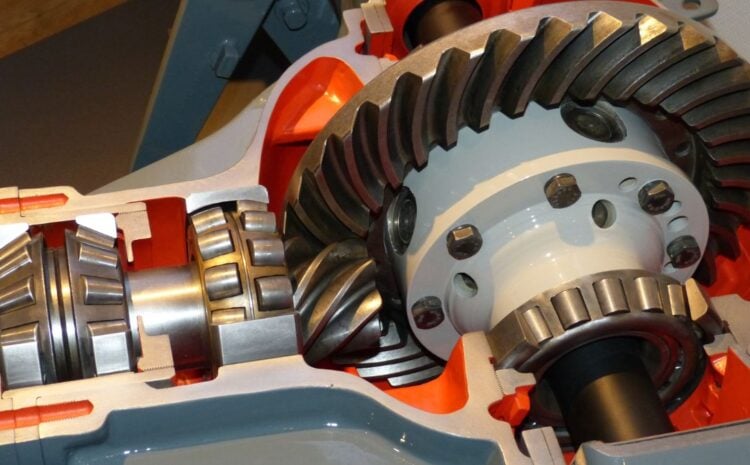
A. Gear Hobbing
People use gear hobbing to remove material from a gear blank and produce the desired gear shape using a rotating cutting tool (the hob). They can use this method for both internal and external gears, and it is most frequently used for cylindrical gears. The ability to quickly and accurately produce gears as well as the ability to create a wide range of gear sizes are two benefits of gear hobbing.
There are several types of hobbing machines that are used in gear cutting. Some of the most common types include vertical hobbing machines, horizontal hobbing machines, and worm hobbing machines. Vertical hobbing machines are typically used for small to medium-sized gears, while horizontal hobbing machines are used for larger gears. Worm hobbing machines are used to create worm gears, which have a unique helical shape.
B. Gear Shaping
People use gear shaping to remove material from a gear blank and produce the desired shape using a rotating cutting tool (the shaper). People can apply this method to both internal and external gears, but they most frequently use it for gears with straight teeth. The ability to create highly precise gears with an excellent surface finish is one of gear shaping’s benefits.
In gear cutting, a variety of shaping machines are employed. Vertical shaping machines and horizontal shaping machines are a couple of the most popular types. People typically use vertical shaping machines for small to medium-sized gears and use horizontal shaping machines for larger gears.
C. Gear Grinding
To shape a gear blank into the desired shape, someone removes material from the blank using a rotating grinding wheel. This method works for both internal and external gears, and people most frequently apply it to highly precise gears with intricate shapes. Gear grinding has its benefits, as it can produce high-precision gears with excellent surface finishes and low noise levels.
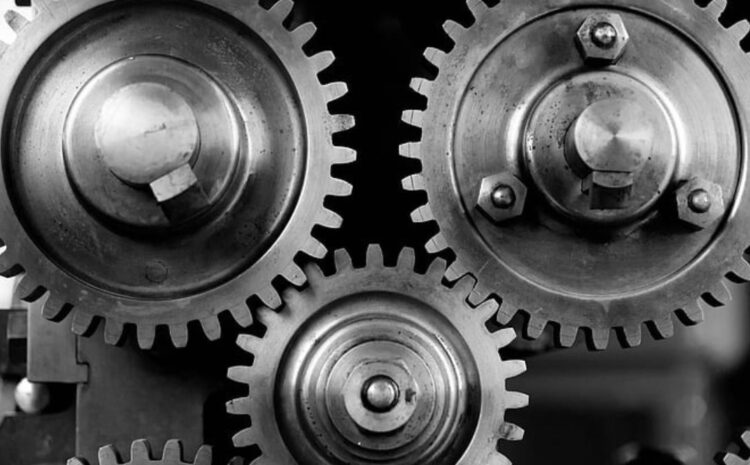
Gear cutting uses a variety of different grinding machine types. Honing, gear lapping, and gear profile grinding machines are a few of the most popular types. Someone grinds gear teeth to a precise shape and size using gear profile grinding machines. They use gear honing machines to remove small amounts of material from gear teeth to smooth out their surface. Finally, they achieve an incredibly smooth surface finish on gear teeth using gear lapping machines.
Applications
People use gear cutting in a wide range of industries, including the automotive, aerospace, and robotics industries.
A. Automotive Industry
The automotive industry relies heavily on gears for the operation of transmissions, differential gears, and other mechanical components. People use gear cutting to produce gears for various applications in the automotive industry, including engine timing gears, transmission gears, and differential gears. They must manufacture these gears with high precision to ensure the proper operation of the vehicle.
B. Aerospace Industry
The aerospace industry also relies heavily on gears for various applications, including aircraft engines, landing gear, and flight control systems. People use gear cutting to produce gears for these applications, and they must manufacture them with extremely high precision to ensure the safe and reliable operation of the aircraft.
C. Robotics Industry
The robotics industry is a rapidly growing industry that relies on gears for various applications, including robot joints and gearboxes. People use gear cutting to produce gears for these applications, and they must manufacture them with high precision to ensure the smooth and accurate movement of the robot.
Advancements
Advancements in technology have led to significant improvements in gear cutting techniques and applications. Two notable advancements are Computer Numerical Control (CNC) technology and 3D printing.
CNC technology has revolutionized gear cutting by enabling highly precise and automated machining. CNC machines use computer programs to control the movement of cutting tools, allowing for highly accurate and repeatable machining. People can use CNC machines for various techniques, including hobbing, shaping, and grinding.
Gear cutting has also benefited greatly from 3D printing. It enables the high-precision production of complex gear shapes, reducing the need for multiple machining operations. It can also be used to make low-volume, specialized gears that would be difficult or expensive to produce using traditional manufacturing techniques.
Conclusion
Gear cutting is a critical process for the manufacturing of gears used in various industries. People commonly use gear hobbing, gear shaping, and gear grinding techniques for gear cutting. They must perform these techniques with high precision to ensure proper gear operation. People use gear cutting in various industries, including the automotive, aerospace, and robotics industries, among others. Advancements in technology, such as CNC and 3D printing, have led to significant improvements in gear cutting techniques and applications. With ongoing advancements in technology, the future of gear cutting looks promising, with the potential for even greater precision and efficiency in gear manufacturing.